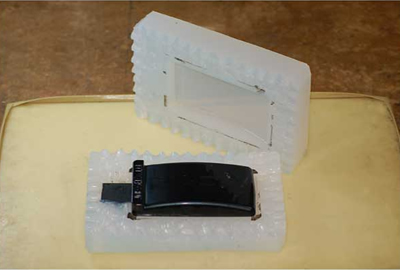
真空注型とは、シリコンでマスターモデルの型を製作し真空に近い機械の中でシリコン型に樹脂を流し込みマスターモデルの複製を製作します。
サンプルに合わせた調色や板金などをインサートして一体での成形も可能です。
小ロットの試作に向いています。
対応材質
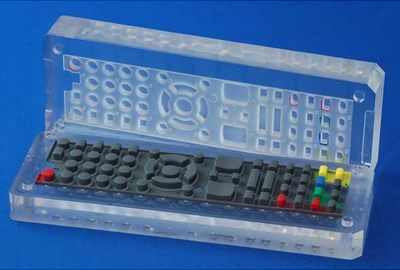
【ウレタン樹脂】
・ABSライク ・PPライク ・アクリルライク ・発泡ウレタン ・エラストマーライク(硬度、調色などご相談ください。)
【シリコン】
・シリコンゴム(硬度20°〜70°、調色などご相談ください。)
※シリコンゴム注型の場合はアクリル型で注型用の型を製作いたします。
真空注型の特徴
マスターモデルについて
- 真空注型では必ず複製したい物の“マスターモデル“が必要になります。主に、切削加工や3Dプリンタで製作します。
- マスターモデルを現物でご用意していただければ、シリコンゴムとの相性もありますが型を作製し注型品を作成できます。
- マスターモデルの対応可能最大サイズは 『 510×430×高さ200mm 』です。
- マスターモデルに磨きや塗装をゴム型製作前に施すことにより、注型品も梨地や光沢などマスターモデルと同じ意匠面にすることが出来ます。
左:マスター(ABS切削後磨き処理し、光沢黒塗装、文字部グレーのシボ塗装)
右:注型品(黒)
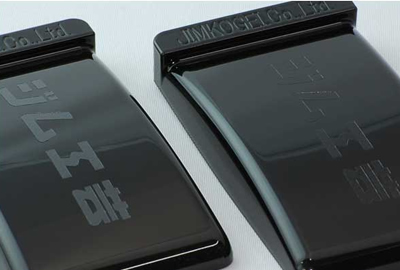
着色注型・インサート注型・2色注型
- 樹脂材料に顔料等を練り込み着色する事が出来ます。サンプルをご提供頂ければ調色することも可能です。
- インサートナットを入れた注型や端子などをインサートした注型も可能です。
- アクリルライク等の硬質樹脂とエラストマーライク等の軟質樹脂など異なる樹脂を一体で注型することも可能です。
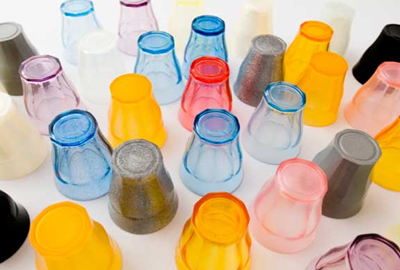
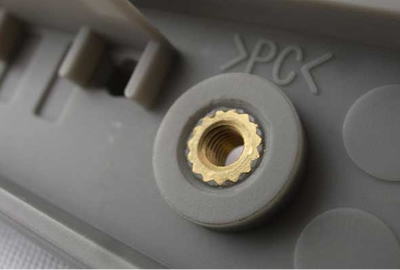
ボディ部(青):アクリルライク
グリップ部(グレー):エラストマーライク
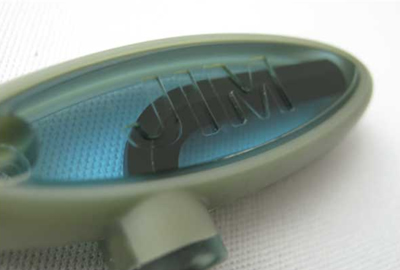
真空注型のメリット・デメリット
- 金型よりも短納期、低コストで製作することができます。
- シリコン型の為、1つの型で10個〜15個までの製作になりますので、小ロットの製作に向いています。
- 切削品ではアンダーカットなどの問題で張り合わせになり強度等の問題がありますが、注型品はシリコン型に柔軟性がある為、 多少のアンダーカットでも一体で製作出来るので強度があります。
また、光を透過して導くような製品(プリズムなど)もマスターモデルは張り合わせでも注型品になると張り合わせ面がなくなり光が透過できるようになります。 - 真空注型では幅広い樹脂のバリエーションがありますが、主成分はウレタン系の熱硬化樹脂になりますので、他の樹脂を選択することは出来ません。
真空注型プロセス
- 1. マスターモデルを用意
- 複製したい元となる形状のもの(マスターモデル)を準備する。
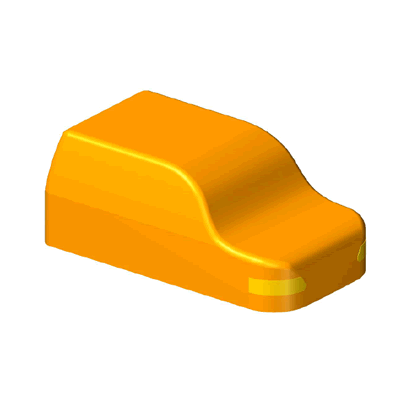
- 2. ゲートの取り付け
- 樹脂の流れ方や仕上がりなどを考慮してゲート(樹脂挿入口)やガス抜き穴の位置を決め、ゲートを取り付ける。
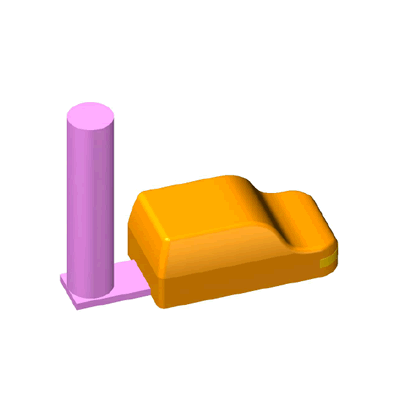
- 3. 型枠を組む
- マスターモデルの大きさに合わせてシリコンを流す型枠を組立てる。
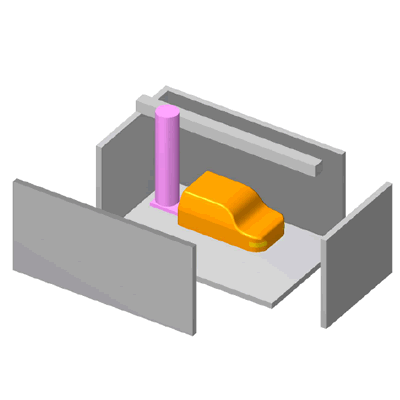
- 4. シリコンゴムの撹拌
- シリコンゴムに硬化剤を入れ十分に撹拌させ、真空脱泡機に入れて脱泡する。
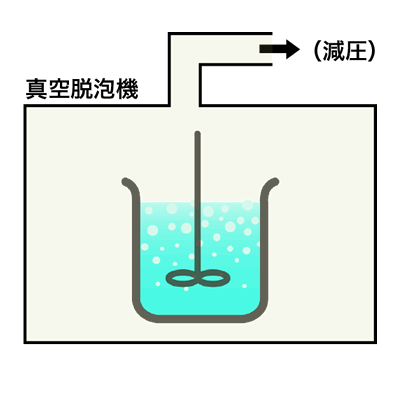
- 5. シリコンゴムの注入
- マスターが完全に埋まるまでシリコンゴムを流し込む。
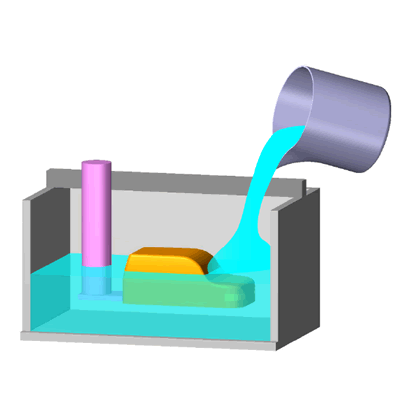
- 6シリコン硬化
- 真空脱泡機に入れ脱泡し、恒温槽の中で硬化させる。
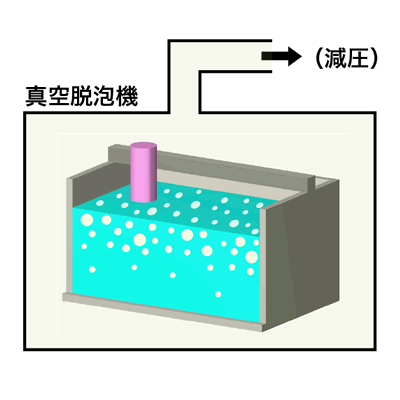
- 7. メスで切り離す
- 型枠から硬化したシリコン型を取り出し、メスで切り開く。
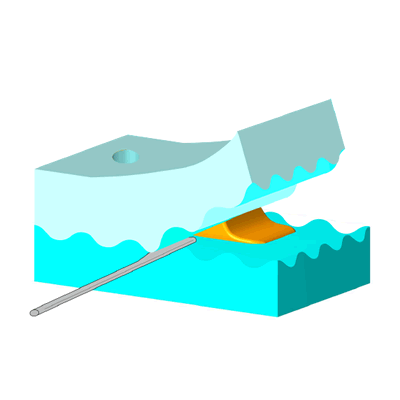
- 8. マスター脱型
- シリコン型を切り離し、マスターモデルを取り出したら真空注型用のシリコン型の完成。
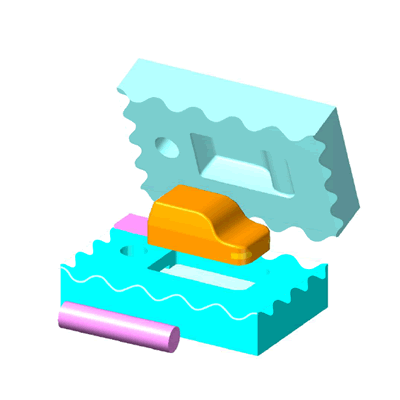
- 9. ゴム型を合わせ固定
- 注型樹脂を流せるように、シリコン型を合わせテープ等でしっかり固定する。
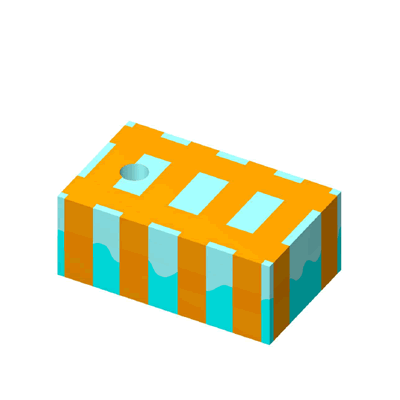
- 10. 樹脂の脱泡
- 計量した注型樹脂を真空脱泡する。
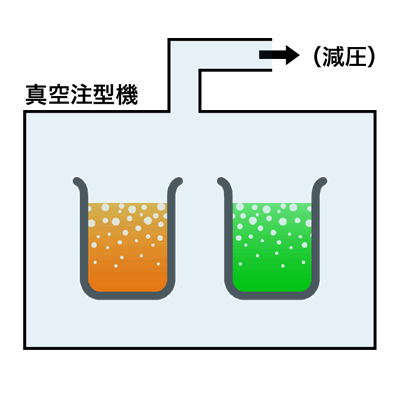
- 11. 樹脂の撹拌・注入
- 真空注型機にシリコン型と脱泡した樹脂をセットし、注型樹脂を撹拌させシリコン型に流し込む。
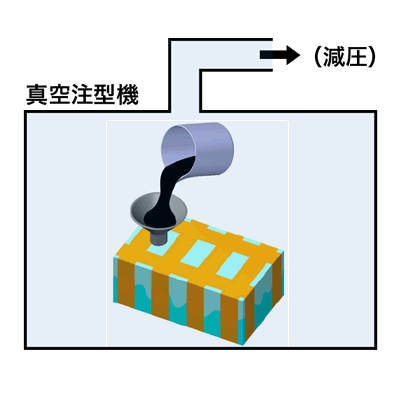
- 12. 樹脂硬化
- 空気圧を戻し、恒温槽にシリコン型を移し指定条件で加熱して樹脂を硬化させる。
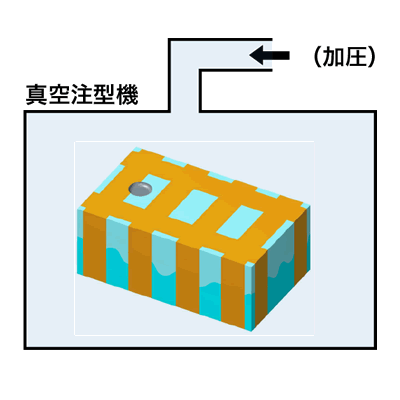
- 13. 脱型
- シリコン型を開き、硬化した製品を取り出す
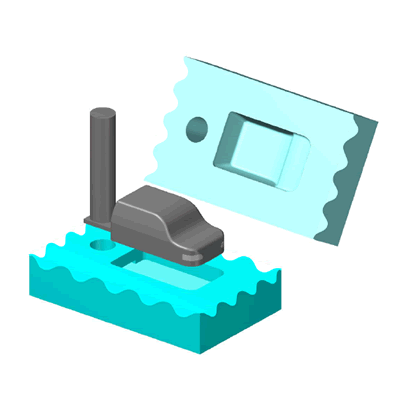
- 14. 仕上げ処理
- ゲートを切断し、ゲートやガス抜き穴のバリをヤスリ等で仕上げる。
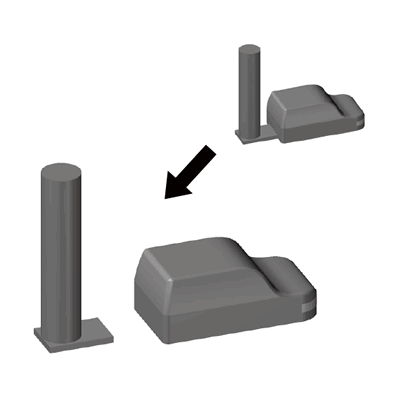
- 15. 完成
- 完成。
⑨〜⑪の工程を繰り返し、1つのシリコン型で10個〜15個製作可能。
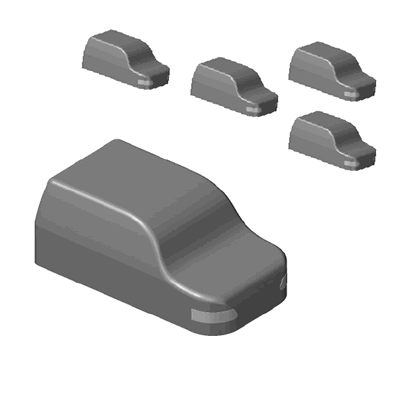